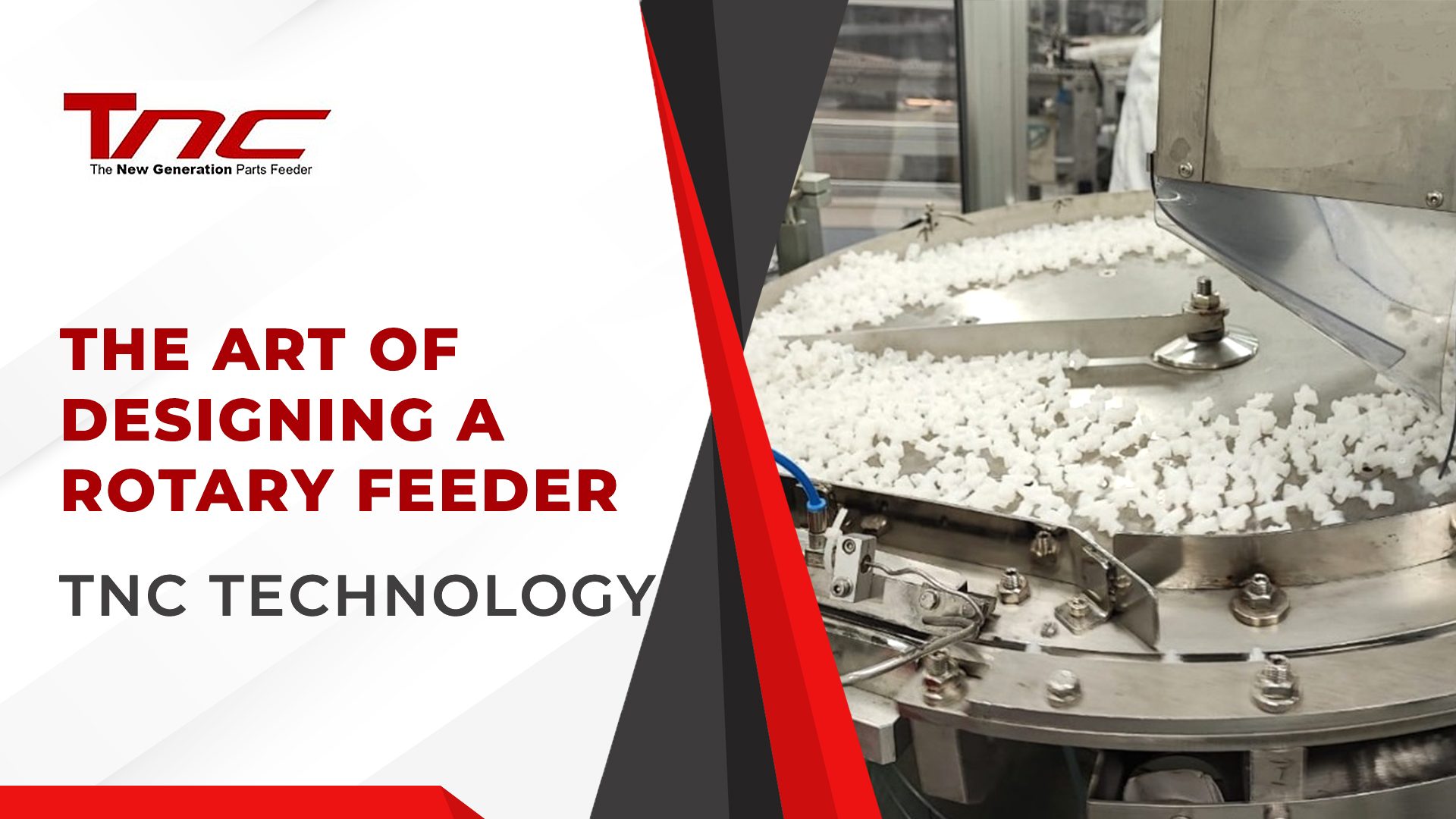
11 Nov The Art of Designing a Rotary Feeder
Ever wondered how a rotary feeder can power so many production lines? It might seem straightforward at first glance, but designing a rotary feeder is no simple task. This vital component does much more than just feed parts into the next stage; it’s meticulously crafted to ensure every part lands in exactly the right spot. In this blog post, we’re taking a closer look at the fascinating design process behind rotary feeders and why these unassuming machines are a big deal in automation.
Understanding the Basics of a Rotary Feeder
A rotary feeder is like a clever conveyor that uses a rotating disk to move parts along. Picture a spinning plate with pockets or grooves that hold each piece securely as it turns. As the disk rotates, parts are smoothly guided into a chute or directly into a machine. The real magic of a good rotary feeder? It’s designed to keep parts moving reliably, without jams or misfeeds, so your process flows without a hitch.
Key Factors in Rotary Feeder Design
Several factors influences come to place when designing a rotary feeder:
Part Geometry:
- Shape: The shape of each part plays a big role in designing the feeder track. Irregular shapes might need customized tracks or even multiple steps to get everything lined up right.
- Size: The part’s size helps decide how big the pockets need to be and sets the pace of the feeder.
- Weight: Heavier parts need more torque to rotate and a stronger force to release them properly.
Material Matters:
- The material type can really impact the track design. For example, fragile pieces might need a softer, non-abrasive track to avoid damage.
- Friction levels also come into play: the right balance keeps the part moving smoothly without any slips or jams.
Feed Rate Goals:
- How quickly you need the parts fed determines the feeder’s speed. Higher feed rates might mean you’ll need a bigger feeder—or even multiple feeders—to keep up.
Orientation Counts:
- Getting the part into the machine in the right position is crucial. The feeder’s design has to make sure each part lands exactly how it should, every time.
The Design Process
The design process for a rotary feeder involves several steps:
- Understanding the Part
The process begins with analyzing the part itself — its shape, material, and weight — to determine the best way to handle it efficiently and securely. - Picking the Right Feeder
Selecting the correct type of feeder machine, whether it’s a disk, indexing, or vibratory feeder, is essential to keep parts flowing smoothly. Each feeder type suits specific needs based on part geometry and required feed rate. - Crafting the Track
The track is custom-designed for each part’s shape and material. A well-crafted track ensures parts stay properly oriented and flow smoothly. During this stage, prototype testing is conducted to verify that parts maintain their alignment and movement without jamming. - Choosing the Drive Mechanism
The drive mechanism, often a stepper or servo motor, allows precise control over speed and positioning. Testing for speed and torque at this stage ensures that the drive mechanism can handle the part’s weight and the desired feed rate without disruptions. - Adding Sensors
Finally, sensors are integrated to monitor part positioning in real-time. These sensors detect issues like jams or misfeeds and allow the system to respond instantly. Sensor calibration and testing confirm that the sensors accurately detect parts, minimizing errors and maintaining a consistent flow.
Each step is tailored to make sure every part flows through the process perfectly!
The Importance of Precision and Reliability
A good rotary feeder can make all the difference in keeping a production line running smoothly. It needs to be precise, reliable, and consistent, ensuring that parts are delivered on time without hiccups. When engineers dig into the details and think through the factors we’ve covered, they can craft rotary feeders that fit perfectly with the unique demands of a manufacturing setup.
In the end, designing a rotary feeder isn’t easy, but it’s incredibly rewarding. With a clear understanding of the essentials and a step-by-step approach, engineers can create feeders that boost productivity and keep those unexpected shutdowns to a minimum.
Ready to take your production line to the next level? At TNC Technology, our expert team is dedicated to designing rotary feeders that align with your unique manufacturing needs. Get in touch with us today to discover how we can enhance your process with precision-engineered solutions!